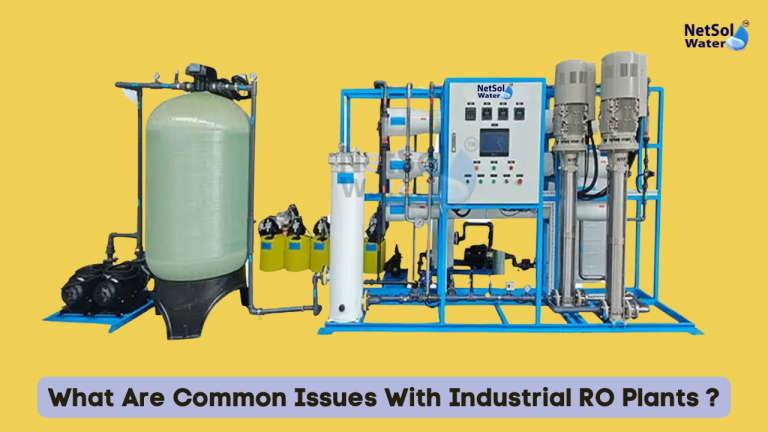
Industrial RO plants filter water for diverse sectors, eliminating impurities to provide high-quality water. RO technology forces water over a semipermeable membrane, effectively removing dissolved particles, organic molecules, and other contaminants. Despite being effective, industrial RO plants often face challenges that affect their performance and longevity. Plant operators, engineers, and maintenance teams need to recognize these difficulties and know how to address them. In this blog we are going to discuss common issues with industrial RO plants and how to solve them.
Membrane Fouling
Membrane fouling attacks industrial RO plants as one of their most widespread concerns. Particles, bacteria, or dissolved chemicals collect on the membrane surface, lowering its permeability and overall system efficiency.
Types of Fouling
1. Organic Fouling
Natural organic materials like humic acids and algal byproducts generate this form of fouling. It can persistently persist and drastically decrease performance over time.
2. Inorganic Scaling
Dissolved minerals like calcium carbonate or silica precipitate and generate this sort of fouling. These minerals build up, generating a hard scale on the membrane surface and impeding water flow.
3. Biofouling
Microorganisms like bacteria and algae colonize the membrane surface, generating a biofilm. This decreases efficiency and can lead to membrane deterioration.
Solutions to Combat Fouling
Operators can implement robust pretreatment methods to limit foulants reaching the membranes. Regular cleaning regimes, including chemical and physical cleaning of membranes, assist sustain performance. Optimizing operational conditions such feed water pH, temperature, and pressure helps limit fouling possibility. Antiscalant dosage reduces mineral scale development on membrane surfaces.
Proactively managing fouling helps plant operators maintain membrane performance and extend their RO plant’s lifespan.
Pressure Vessel Integrity
Pressure vessels house membrane elements and resist high working pressures in RO plants. Issues with pressure vessel integrity can limit efficiency, taint water, and present safety issues.
Common Pressure Vessel Problems
1. O-ring Failures
Degraded or incorrectly installed O-rings produce leaks, allowing feed water to bypass membranes and contaminate the permeate.
2. End Cap Damage
Cracked or warped end caps damage seals, leading to leaks or uneven pressure distribution.
3. Vessel Corrosion
Harsh chemicals or incorrect material selection erode pressure vessel bodies, reducing their structural integrity.
Maintaining Pressure Vessel Health
Operators should implement frequent inspection schedules to check for wear, corrosion, or damage. Proper installation and maintenance of O-rings and end caps, following manufacturer requirements, prevent difficulties. Choosing appropriate pressure vessel materials for specified feed water chemistry and operating conditions improves lifetime. Applying proper coatings or linings protects vessel interiors from corrosive elements.
Maintaining pressure vessel integrity minimizes costly downtime and guarantees RO plants safety and reliability.
High Energy Consumption
Industrial RO plants consume substantial amounts of electricity, considerably increasing operational expenses. Addressing this issue maintains economic viability and decreases environmental effect.
Factors Contributing to High Energy Use
1. Inefficient Pumps
Outdated or poorly maintained high-pressure pumps cost unnecessary energy.
2. Suboptimal System Design
Inefficient pipework, large equipment, or inadequate flow distribution leads to excessive energy losses.
3. Membrane Fouling
Fouled membranes require greater operating pressures, increasing energy usage.
Strategies for Energy Optimization
Plant operators can implement energy recovery devices like pressure exchangers or turbines to recover energy from the concentrate stream. Upgrading to high-efficiency, variable-speed pumps optimizes energy utilization. Thorough analysis of RO plant layouts finds and eliminates inefficiencies in piping, valves, and equipment sizing. Regular maintenance maintains all components working at peak efficiency. Newer, low-energy membranes achieve the same permeate quality at lower working pressures.
Focusing on energy efficiency decreases operational expenses and enhances RO plants sustainability.
Inadequate Pretreatment
Effective pretreatment protects RO membranes and maintains maximum system performance. Inadequate pretreatment leads to quick membrane fouling, lower efficiency, and increased operational expenses.
Consequences of Poor Pretreatment
1. Accelerated Membrane Fouling
Insufficient removal of suspended particles, organic matter, and other pollutants quickly overwhelms RO membranes.
2. Increased Chemical Usage
Poor pretreatment needs more frequent membrane cleaning, resulting to higher chemical consumption and possibly membrane degradation.
3. Reduced System Lifespan
Inadequate pretreatment’s cumulative effects drastically limit RO membranes and other system components operational life.
Improving Pretreatment Effectiveness
Plant operators should do feed water analysis to detect potential foulants and alter pretreatment techniques. Implementing multi-stage filtration addresses numerous pollutants. Optimizing chemical dosage ensures optimal treatment based on feed water quality and system needs. Regular maintenance and service of filter systems, chemical dosing pumps, and other pretreatment components maintains effectiveness. Advanced pretreatment procedures like electrocoagulation or dissolved air flotation can benefit problematic feed water sources.
Investing in thorough pretreatment protects RO plants and increases their longevity and efficiency.
Common Operational Mistakes
1. Inadequate Operator Training
Insufficient awareness of RO concepts and system operation results in poor decision-making and inferior performance.
2. Inconsistent Monitoring
Failure to consistently monitor important parameters such feed water quality, pressure differentials, and permeate quality leads to missed early warning signals of system faults.
3. Improper Startup and Shutdown Procedures
Incorrect practices during system startup or shutdown cause membrane damage, hydraulic shocks, and other difficulties.
Enhancing Operational Excellence
Facilities should invest in thorough training programs for operators and execute continuing education. Robust monitoring and control systems track important parameters and notify operators about potential issues. Detailed SOPs for all elements of RO plant operation, including startup, shutdown, and maintenance, assure consistency.
Conclusion
Industrial RO plants require careful management and maintenance to function at peak performance. Understanding and addressing typical concerns guarantees RO plant longevity and reliability. Applying the solutions and best practices indicated here helps industrial establishments optimize their RO plants, save operational costs, and assure consistent high-quality water supply for their processes.
To explore customised commercial RO plants, Industrial RO plants, ETP or STP solutions for your needs in your areas and nearby regions, contact Netsol Water at:
Phone: +91-965-060-8473
Email: enquiry@netsolwater.com