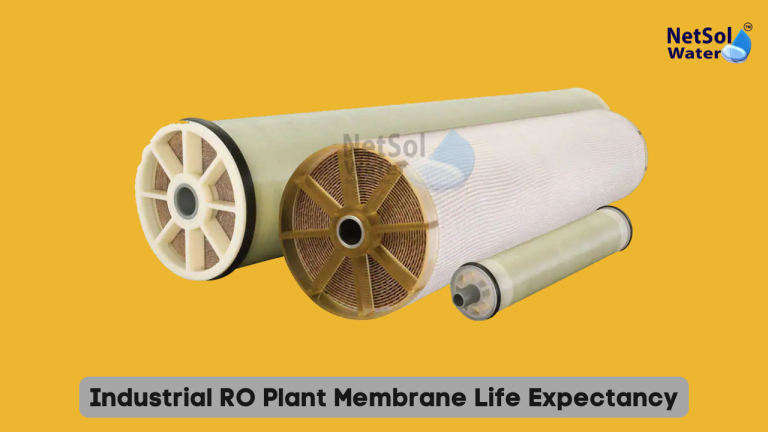
Industrial RO plants are very essential in many ways for treating huge amounts of water for different kinds of industries. The most important part of the plant is a membrane, and it filters all impurities and provides clean usable water, but like everything, RO membranes also have a lifespan. Several factors affect the performance and life of such membranes, thus with proper care it can last longer and work efficiently.In this blog, we will discuss industrial ro plant membrane life expectancy, what affects the life of an RO membrane, how to extend the lifespan, and common practices that can help a membrane stay healthy for a longer period.
What Affects the Life of an RO Membrane?
The average lifespan of an industrial RO membrane is up to 5 years, but it generally lasts from 2 to 5 years. There are many factors affecting the extension of how long it will last.
1) Water Quality
The most important factor is the quality of water being treated. Poor quality water, with an ample amount of impurities like dirt, calcium, or iron, will mean high stress on the membrane, thereby wearing it out faster. Pre-treatment, either by filtering or adding chemicals, can improve the quality of water and prevent fouling.
2) Membrane Fouling
Periodically, fouling impurities such as scale and organic matter will attach to the membrane surface. Fouling decreases the membrane in efficiency for filtering water and also their life span. Preventing the fouling can be achieved by regular cleaning with proper antiscalants and biocides.
3) Pressure and Flow Rate
Industrial RO plants need high pressure to push water through the membrane. This could damage the membrane when it is too high, too low, or uneven. Proper pressure and flow mean efficient functioning of the system so that the membrane is not overstressed.
4) Chemical Damage
Cleanser or antiscalants can also be hazardous to membranes if the operating personnel uses the wrong dosage or has the poor practice of using too much of these chemicals. It is necessary to apply the right chemicals as well as the correct quantities, in order not to harm the membrane. Chemical safeguard must always follow the instructions given by the manufacturer in how to use them.
5) System Maintenance
This is a big factor in the life expectancy of the RO membranes. Careful cleaning of the system, proper performance check, and timely response to any issues that may cause reduction in the life of the membrane will add up to the total life of the membrane.
Signs of a Failing Membrane
Membranes also have lifecycles whether you care for them or not. Here are some common signs that an RO membrane is close to being at the end of their life.
1) Water quality declining: The water coming from the filter system will be dirty with more impurities as the membrane has lost its ability to shut them out.
2) Less water output: The volume of water produced by the system will decrease largely due to blockage or deterioration.
3) Increased pressure: Sometimes the system will need higher pressure to pump water through the membrane which is an indication of fouling or blockage.
4) Frequent cleaning: If you find yourself cleaning the system a lot, it means the membrane is not functioning as it should.
Ways of increasing the useful life of the RO membranes
While it is true that the normal life expectancy of RO membranes is short, they can however, serve severally folds longer if only the best practices highlighted below are followed: Here are a few tips:
a) Pre-treatment of Water:
Before water reaches the RO membrane, it should have been subjected to some procedure known as pre-treatment. The pre-treatment could involve filters that remove big particles like dirt or sand and there could be chemicals that could neutralize scaling agents or bacteria. The quality of water entering the RO plant improves and less work has to be done by the membrane to filter out the water, hence prolonging its life.
b) Regular Cleaning:
Regular cleaning is very essential to prevent fouling and deposition on the membrane. The various types of cleaning agents depend on the type of fouling; for instance, acidic cleaners are used for scaling and alkaline cleaners for organic fouling. Cleaning the system at regular, predefined intervals ensures that the membrane is kept clear of injurious depositions.
c) Monitor Performance
This keeps an eye on the potential problems that are likely to occur before they damage the system. Check for the following:
- Water flow rate: Drops significantly; this may indicate that the membrane is clogged.
- Water quality: Check the TDS level in the water. Increasing TDS may indicate that it is not filtering water as effectively as before.
- Pressure: Pressure changes can be a sign of problems in a membrane malfunction or the system malfunctioning.
d) Use Antiscalants and Biocides
Antiscalants prevent scale formation, one of the biggest dangers to RO membranes. Biocides prevent bacterial and other microorganism growth. When applied correctly, they prevent fouling as well as extend the life cycle of the membrane
e) Maintain proper pressure
Set the pressure inside the RO plant according to the manufacturer’s recommended pressure levels. Too much pressure may damage, and less pressure results in inefficient filtration with associated fouling.
f) Replace Prefilters regularly
The system has pre-filters, which are used in order to capture larger particles before reaching the membrane. The more dirt collected by the pre-filters, the less effective it will work. This might result in passing some impurities to the membrane, and this is the risk of replacement pre-filtering regularly to protect the membrane.
g) Role of System Design
Design of the RO plant also determines membrane life. A well-designed system should have elements such as correct pressure regulation, flow regulation, and cleaning options that are protecting the membrane. Expert professionals in installation that understand the needs of your business should be engaged in the installation process of an industrial RO plant. The professionals will ensure that the system they design maximizes membrane life.
Conclusion
The life span of an industrial membrane depends on several factors like quality water, fouling pressure, and maintenance.
Regular monitoring, proper use of chemicals, and scheduled maintenance form the backbone to ensure a maximum return out of an RO membrane. With proper care and the right approach, an industrial RO membrane could easily work for several years in delivering reliable and efficient water treatment for your business.
Remember, proper RO plant maintenance ensures not only the prolongation of membrane life. But also the optimization of overall efficiency in the plant and saves you valuable time and money down the road.
Do you need an advice or assistance on selecting the best water and waste water treatment unit? We have solutions for all your problems!
Let us know your problem, our experts will make sure that it goes away.
For an assistance or related query,
Call on +91-965-060-8473
Or write us at enquiry@netsolwater.com