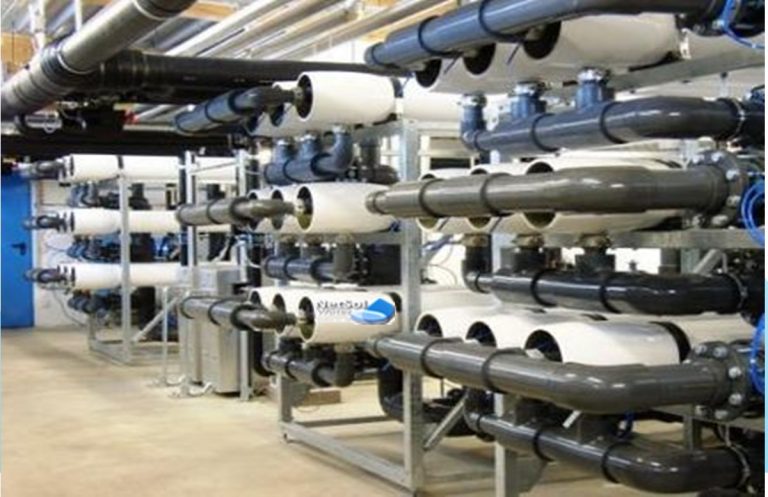
Membrane Fouling in Reverse Osmosis Plants are used extensively in industrial and municipal water use and treatment facilities for desalination and water purification. Since the late 1970s and even today, maintaining the productivity of RO plants as continuous water purification systems has been a serious technological issue.
Mechanisms of Membrane Fouling in Reverse Osmosis Plants
When permeate water is produced, feed waters to RO systems are typically concentrated by a ratio of 2 to 10 (50 percent to 90 percent recovery). With membranes, comes their fouling as well. For ease of categorization, fouling in RO Membranes can be divided into three categories.
- Scaling
Crystals may deposit and grow in the flow channels and membrane surface of the RO elements when the solubility limitations of different dissolved salts in the concentrate stream are surpassed. Calcium carbonate, calcium sulphates, strontium and barium, as well as calcium fluoride and calcium phosphate, are the most prevalent types of scales. Scaling requires the formation of crystal seeds in the super-saturated concentration. The seed crystals could develop into recognisable forms like plates, flakes, prisms or needles, or they could stay as finely distributed particles that are either visible to the human eye or undetectable.
Antiscalants function by preventing the development of these seed crystals and requiring the RO concentrate to stay for a while in a supersaturated state. This is known as threshold inhibition. Low concentrations of antiscalants while keeping high super-concentrations in the RO concentrate effectively perform the duty of inhibiting scale growth.
- Colloidal fouling
Smaller than 1.0 micron in size colloidal particles might cause membrane fouling. They are almost impossible to identify by turbidity and silt density index (SDI) measures since they are invisible to the human eye. Colloidal particles are not retained by the 0.45 micron filters used in SDI measurements. In fact, even after pre-treatment with microfiltration and ultrafiltration in RO systems, colloidal particles continue to pass, severely fouling the RO membranes.
Table showing different RO Plants Fouling
RO Foulant | Traditional Pre-treatment |
1. Calcium Carbonate | Acidification to lower LSI, then with antiscalant to maximum LSI |
2. Iron, manganese | Oxidation/filtration: Greensand, manganese dioxide, catalytic oxidation |
3. Silica: Reactive | Lime, Ion-Exchange |
Non-reactive | None |
4. Calcium Sulfate | Lime, Ion-Exchange |
5. Strontium Sulfate | Ion-Exchange |
6. Barium Sulfate | Ion-Exchange |
7. Calcium Fluoride | Lime, Ion-Exchange |
8. Colloidal Organic Matter and Sulfur | UF, MF, coagulation/clarification/ MMF, slow sand and carbon filter |
Increased concentration of salt, compaction, flocculation, surface contacts and other physical and chemical variables can cause colloidal particles already present in feedwater to assemble and cling to the membrane and brine flow channels.
Colloid Formation
1: Colloids can form composite, inorganic or organic flocs. Polymerization causes dissolved ionic – ferric, aluminium and calcium hydroxides as well as silicic acid to expand to larger particle sizes.
2: Organic and inorganic polymers undergo cross-linking to form gels and amorphous foulants that are frequently observed on membranes. This kind of foulant is typically composed of biotic waste like polysaccharides and dead cellular material.
It has become clear through the resolution of several fouling issues in operational RO plants that overuse and apply pretreatment chemicals, which worsen the propensity of natural colloids in RO feed waters to congeal and become foulants. Recent developments in anticoagulants offer hope for preventing this fouling process.
Biofouling
It is a prominent source of fouling. The development and agglomeration of microorganisms occurs in all water treatment and distribution systems. Microorganisms can occasionally develop explosively in Commercial RO raw waters because of the moderate temperatures and low nutrition levels. In the course of an 8-hour shift, bacteria that can divide their cells every 20 minutes can increase from a typical count per unit volume of water to millions. This fouling mechanism is distinct and poses a severe risk to the functioning of Commercial RO Plants since bacteria have a propensity to release polymers that anchor themselves to surfaces to assist growth of the biofilm. The threat is increased by how challenging it is to completely treat and remove the biofilm from the membrane surface.
To learn more about industrial RO plant membrane cleaning processes, call us at +91-9650608473 or send an email to enquiry@netsolwater.com